The GRACE Satellites

Bild: Airbus
The two satellites of the first GRACE mission were largely based on the design of GFZ's earlier CHAMP (Challenging Mini-Satellite) mission, which was launched in July 2000 and operated for over 10 years to measure both the Earth’s gravity and magnetic fields. The CHAMP platform was designed and built on behalf of the GFZ by Daimler Chrysler Aerospace Jena Optronik GmbH (DJO) in cooperation with Dornier Satellitensysteme GmbH (formerly DSS, now Airbus) and Raumfahrt und Umwelttechnik GmbH (RST). CHAMP was the prototype for a number of subsequent Airbus missions, such as TerraSAR-X (DLR, launched in 2007), TanDEM-X (DLR, launched in 2010) or Swarm (ESA, launched in 2013). The technology known as "Flexbus" is based on a number of outstanding platform features that were developed and realised in particular for gravity field missions and for this reason were commissioned by JPL/NASA for GRACE (2002-2016) and GRACE-FO (since 2018) to Airbus in Immenstaad.
The satellites for the follow-up mission GRACE-C (to be launched in 2028) will also be built by Airbus again. This is because the satellites need to have the following special characteristics:
- "quiet satellites": The two satellites are only extremely slightly affected by seismic micro-disturbances. They also have excellent electromagnetic compatibility, i.e. no component is disturbed by unwanted electrical or electromagnetic effects. Finally, the centre of mass of each satellite, which may change over time, e.g. due to asymmetrical emptying of the two fuel tanks, can be kept constant to 0.1 millimetres by adjusting test masses in orbit.
- "Thermal stability": The temperature can be kept stable at 0.1° Celsius during the whole orbit on both satellites to avoid disruptive changes in the structure and misinterpretation of the distance measurements between the satellites. This is achieved by regularly switching on heating elements, and by dissipating the resulting heat to the outside via a specially developed foil on the bottom of the satellites.
- "Mechanical stability": For similar reasons, the structure of the two satellites must be extremely stable so that any changes over one orbit are less than 2 micrometres. This is achieved by making the structure out of CFRP (Carbon Fiber Reinforced Polymer). In addition, ceramic material (silicon carbide) is used to connect the star cameras to the structure for high-precision alignment of the satellites in space.
- "Alignment accuracy": For the distance measurement between the satellites, both spacecraft must be continuously and precisely aligned with each other. Various instruments on board the two satellites, such as GPS receivers, star camera systems or high-precision gyro stabilisers, help to realise the necessary accuracy of 140 microrads (which corresponds to just 28 metres of alignment error at a distance of 200 kilometres).
- "Mission duration": In order to realise the mission duration of at least 5 years, all essential systems (attitude and temperature control, power supply, data storage, etc.) are duplicated on the platform and there are no unwanted interconnections between them. All systems are designed to minimise fuel consumption. This particularly includes an aerodynamic design of the satellite structure. This has resulted in GRACE having a lifetime of more than 15 years. GRACE-FO already entered its additional mission phase followin the five-year launch anniversary in May 2023.
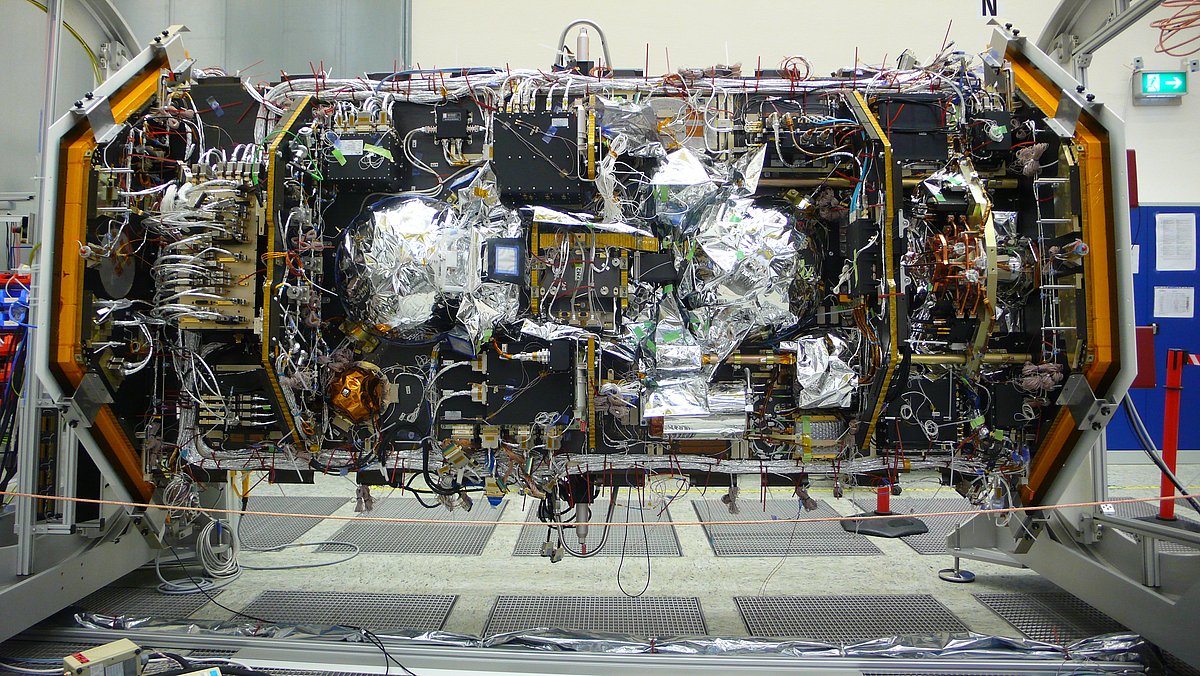
Foto: Airbus
Distance measurement
The continuous measurement of the distance between the two GRACE and GRACE-FO satellites is the primary observation for measuring temporal and spatial changes in the gravity field. The satellites trailing each other at a distance of around 200 kilometres are attracted by the Earth slightly differently - sometimes more strongly and sometimes more weakly - depending on how much mass is underneath them. This leads to a continuous small change in the distance between the satellites. The primary instrument for measuring this distance on both missions is the very precise distance measuring system HAIRS (High Accuracy Inter-satellite Ranging System) developed by NASA's Jet Propulsion Laboratory (JPL) especially for GRACE, whose accuracy is a few thousandths of a millimetre. This corresponds to about one tenth of the diameter of a human hair.
A Laser Ranging Interferometer (LRI) is also operated on GRACE-FO as a technology demonstrator for future gravity field missions. The LRI is a collaboration between JPL and German partners under the leadership of the Max Planck Institute for Gravitational Physics (Albert Einstein Institute, AEI) in Hannover. The LRI concept, its prototypes and the technical specifications originate from the AEI, whose researchers were intensively involved in the development and testing of the flight hardware.
The German contributions to the LRI comprise the entire optical system, consisting of
- a triple mirror assembly (TMA) manufactured by Hensoldt (formerly Zeiss) in Oberkochen,
- the optical bench assembly (OBA) from SpaceTech GmbH in Immenstaad, which was responsible for the entire German LRI contribution on the industry side including also the optoelectronics from the German Aerospace Center (DLR) in Berlin-Adlershof, and electronic assemblies from Apcon AeroSpace & Defence in Neubiberg near Munich,
- calibration instruments developed and supplied by the DLR Institute of Space Systems in Bremen,
- the LRI electronics (Optical Bench Electronics, OBE) for which JPL is responsible, the LRI processor (Laser Ranging Processor, LRP), the optical frequency reference (Cavity), and the procurement of the laser from Tesat Spacecom GmbH & Co. KG in Backnang near Stuttgart.
The LRI exceeded all expectations at GRACE-FO. Since its first commissioning on 14 June 2018, it has delivered measurement data virtually continuously, unless operational reasons on the satellites (e.g. manoeuvres or special in-flight tests) prevented the laser operations. With just 2 nanometres, the high-frequency measurement noise of the LRI is significantly lower than its specification of 60 nm and thus right of the order of magnitude of the thickness of a DNA strand This is realized in flight at a distance of about 200 kilometres and a satellite speed of roughly 27,000 km/h. It has been confirmed also that high-frequency (small-scale) signatures in the Earth's gravitational fieldThe Earth's gravitational field is made up of the Earth's gravitational pull and the latitude-dependent centrifugal acceleration caused by the Earth's rotation. The matter in and on the Earth is not evenly distributed. Water, loose sediments (such as... can be determined much more accurately with the LRI. The laser system has thus proven to be clearly superior to the microwave method and will therefore be routinely used instead of microwave interferometers on the future gravity missions.
Text: Prof. Dr. Frank Flechtner, GFZ
Further information
- Airbus Website
- Interferometry in space at the Max Planck Institute for Gravitational Physics
- SpaceTech Website
Further reading
- Sheard B. et al. (2012): Intersatellite Laser Ranging Instrument for the GRACE Follow-On Mission, J. Geod., doi: 10.1007/s00190-012-0566-3.
- Abich K. et al. (2019): In-Orbit Performance of the GRACE Follow-On Laser Ranging Interferometer, Phys. Rev. Lett., doi: 10.1103/PhysRevLett.123.031101.
- Kornfeld, Richard P., Arnold, Bradford W., Gross, Michael A., Dahya, Neil T., Klipstein, William M., Gath, Peter F., and Bettadpur, Srinivas, 2023. GRACE-FO: The Gravity Recovery and Climate Experiment Follow-On Mission. Journal of Spacecraft and Rockets, 60(1):1–1, doi:10.2514/1.A34326.c1.